
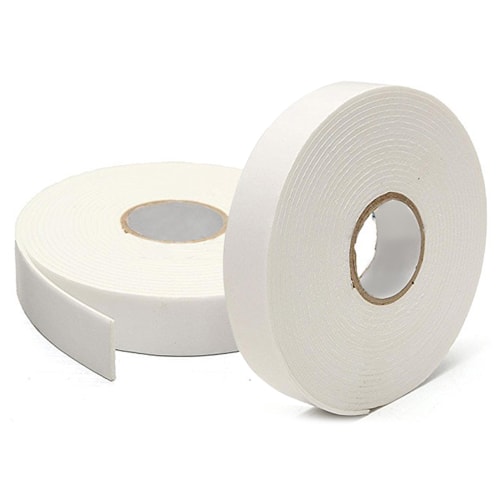
This ‘shock absorbing’ effect mitigates dot gain and any bouncing in the cylinders that can show as ‘banding’ or ‘gear marks’ in the print. For example, for printing solids, a hard foam or even a film should be used to promote proper ink density and distribution, while for printing fine screens with high line screen plates, softer tapes provide the best cushioning effect to act as a shock absorber. UK managing director, Steve Plastow, said that when evaluating tapes, it is important to understand how the hardness levels of the foam correlate to specific print designs. With five different levels of hardness, tesa’s Softprintrange is available in hard, medium-hard, medium, soft and x-soft, each tailored to the individual requirements, whether used for short print jobs, with the associated high number of changeovers, or long printing jobs, which require a particularly strong bonding of the plate for fine screens, which require soft plate mounting tapes, or jobs with high print speeds and complex designs. The HP 5 range is available in different foam hardnesses to permit fine process work as well as dense ink coverage.įor label printing, the company has the DuploFlex 3 and 4 ranges, ideal for printing jobs in a thickness range of 0.38 mm and 0.44 mm and coping with printed images with fine runs as well as dense ink coverage and clean lettering. In addition, it effectively counteracts machine vibrations and prevents vibration marks, which distort the printed image. Compared with conventional foams, the polymer foam also has a very high degree of stability and regains its original form perfectly. An even greater distribution of pressure is guaranteed by the smaller uniform cell size structure. The high performance polymer foam (HP) employed plays a key role. The DuploFlex HP 5 product is used for difficult and demanding printing jobs. One UK customer recently ran a multi-colour line and process job for 1.9 million metres without the need to change tape. The compression features and recovery of these products make them suitable for all plate types and images, from short to long runs.
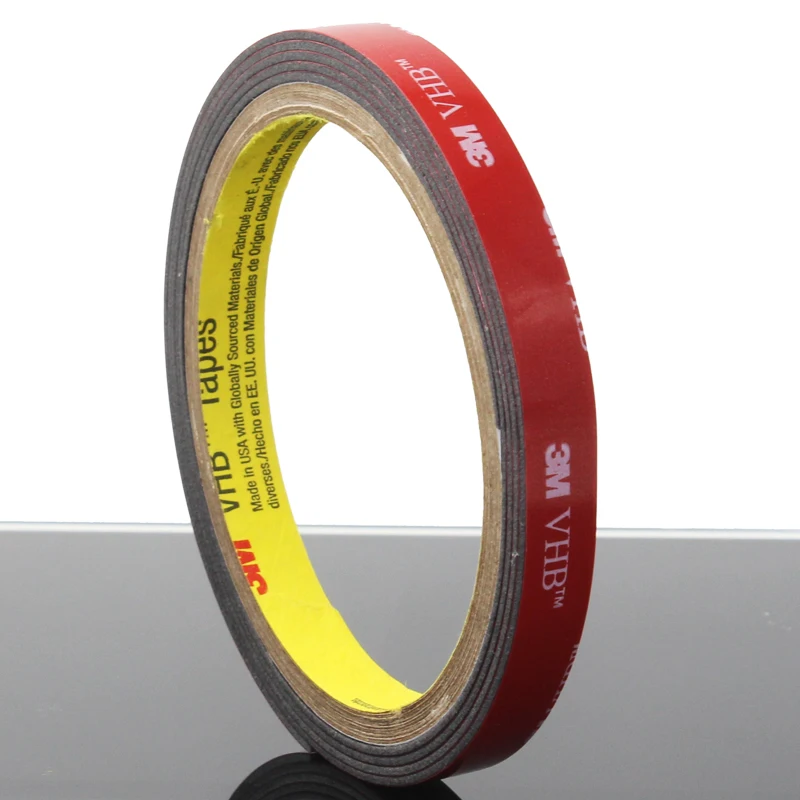
The basic DuploFlex 5 range consists of several compressible adhesive tapes that differ in terms of foam hardness and adhesive strength. Additionally every linear metre of foam mounting tape passes through a thickness measurement unit to ensure it conforms to a stringent thickness tolerance.’ ‘This construction is proven to support all these variables. ‘With ever increasing image detail/complexity, finer screens, more lines per inch, finer aniloxes, higher densities, the plate mount tape comes under a lot of pressure (excuse pun) to perform,’ said Bob Drew, national sales manager, graphics products. Its DuploFlex range of plate mounting tapes is manufactured with a double-sided flexible PE-reinforcement system which offers superior results in the transfer of the printed image. Lohmann Technologies UK, a subsidiary of the Lohmann Adhesive Tape Group, explained that it is well aware of these special requirements and what can be achieved. It cushions vibrations and further accommodates the varying degrees of hardness of the numerous printing plate variables. The adhesive foam tape also acts as a substructure under the printing plate, allowing accurate transfer of the plate image to the substrate. The adhesive requirements are simple: bond to the sleeves/cylinders and plates as securely as possible during printing to completely eliminate any possibility of plate edge lifting or bubbling and when the job is done, remove easily. The adhesive can be the distinguishing factor between having to clean off residues when the job is stripped, or having the tape removed cleanly with little to no required cleaning, said 3M. The latter should be possible without leaving any residue on the plate or cylinder so that job changes can be done as quickly as possible. Balancing the tack level of this tape is crucial as it both needs to hold the plate in place, ensuring there is no movement during printing, and also has to be easy to remove when demounting at the end of the job. Tapes for flexo printing are precision engineered double-sided adhesive structures consisting of several layers of material, including compressible foam, reinforcement film, release liner as well as the actual adhesive. Although it may seem that the tape is simply there to stick the plate to the printing cylinder, the increased demands from the flexo printing process, such as higher running speeds, faster changeovers and cost reduction, mean that the importance of this component cannot be overlooked. Deciding which tape is right for each print job is a significant factor in the quest for efficiency and process reliability.
